Contact Your NewwaySMTC Representative Now! [email protected]
The production of carrier tape mold and the reasons for production errors
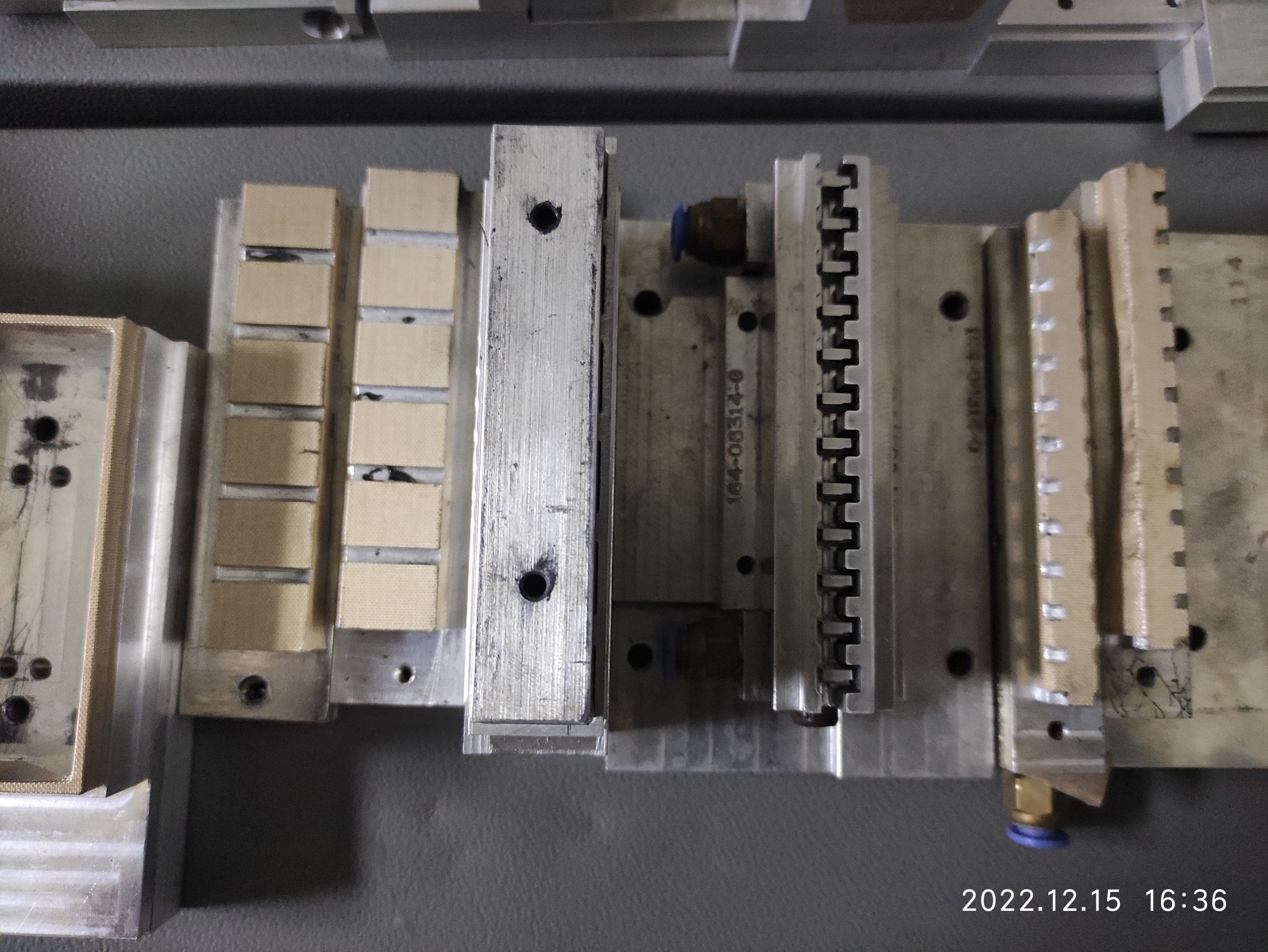
Carrier tape mold can be designed according to the carrier tape punching mold structure, to meet the different requirements of customers to the market, developed a special full cavity positioning punching mold for small gap carrier tape, accurate positioning, simple operation, no need to adjust any parameters, cavity P2 value accurate in place, solve the troubles of many carrier tape manufacturers.
The life of the punching mold is long, and the replacement of different specifications of the base plate can meet the multiple uses of a mold, not only high efficiency and save money. The strip molding mold has the feature of multiple cavities in one mold, and can generate about 20 cavities in one compression molding.
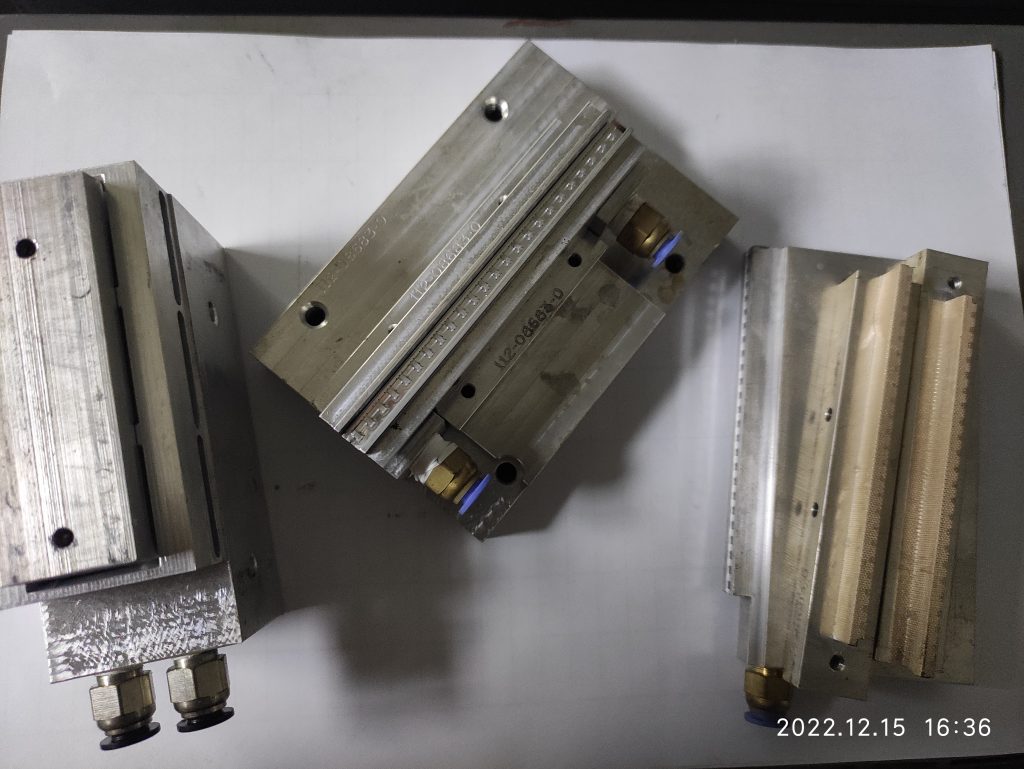
Strip mold production process of progressive mold technology
SMD carrier tape mold this trial mold mechanical press development trend is the use of multi-link tension press, which is equipped with CNC hydraulic tension pad, with parameter setting and state memory function, body manufacturing in the development of the progressive punching mold rapidly.
The processing of rotor and stator plates with progressive punching molds or combination punching molds on automatic punching machines, or their application in insert operations, are well known stamping technologies.
In recent years, progressive combination punching molds have begun to be used more and more extensively in body manufacturing, where progressive molds are used to process coils directly into formed parts and drawn parts. The parts processed are also getting larger and larger, eliminating the need to use multi-station presses and sets of molds to produce the necessary series of subsequent processes such as plate shearing, oiling, and slab transport. Carrier strip molds have been commonly used in the U.S. automotive industry, with the advantages of high productivity, low mold costs, unimportant sheet shear, and 30% savings compared to step molds used on multi-station presses, but the application of progressive combination mold technology is limited by the depth of stretching, guiding and surface hardening of the material at the edge of the transported strip, and is mainly used for simple parts with a relatively shallow depth of stretching, so it cannot completely replace multi-station presses The majority of parts should be preferably processed on multi-station presses.
The importance of strip tooling in production
The design of carrier tape mold is the basic production process equipment for industrial production, and the mold industry is an important part of machinery industry and high-tech industry.
Failure in the manufacturing process of carrier tape mould
The carrier tape mold pouring system is defective. The runner is too small, too thin or too long, which increases the fluid resistance. Can fill cavities
But can not fill other cavities, the diameter of the runner should be increased in order to reduce the pressure drop of the melt flowing to the unend of the runner, the cavity gate farther away from the main flow channel should be increased so that the injection pressure and flow rate to reach each cavity its own same.
The design of carrier tape mold is not reasonable. The mold is too complicated, with many turning points, incorrect choice of inlet, too narrow flow channel, insufficient number of gates or inappropriate form.
What are the mistakes of carrier tape mold making process?
1. Improper adjustment of feeding material, lack of material or more material, inaccurate dosing measurement or abnormal operation of dosing control system, abnormal injection cycle due to injection machine or mold or operating conditions, small back pressure before molding or small granularity checking in the barrel are
It may lead to the lack of material.
2. Low injection pressure, short injection time, premature withdrawal of column cold or screw, high viscosity of molten plastic at low working temperature, poor fluidity, should be injected at high pressure and high speed.
3. Injection speed huff, injection speed for some complex shapes, thickness changes, long process flow products, and toughened ABS and other higher viscosity plastics, significant, when the product can not be filled with high pressure, should consider high-speed injection
injection, to overcome the unsatisfactory problems.
4. material temperature is too low, the front end of the barrel temperature is low, speak into the cavity of the melt viscosity due to the cooling effect of the mold and prematurely rise to the extent that it is difficult to flow, hindering the distal end of the filling: the rear of the barrel temperature is low, high viscosity, difficult flow, shading
As a result, it seems that the pressure shown on the pressure gauge is sufficient, but in fact the melt enters the cavity with low pressure and low speed, and the nozzle temperature is low, probably because the contact time between the nozzle and the cold mold is too long when fixing the material, and the execution is scattered.
Or because the nozzle heating ring heating is not sufficient or c bad cause material temperature low will block the cold mold speak material channel:If the mold is not well cold material, please use self-locking clarion nozzle, and use the post-feed program, the nozzle can keep the necessary conditions, just open
The temperature of the nozzle is too low when the machine is on. Sometimes you can make the field flame gun for external heating to accelerate the nozzle heating
5. raw materials, poor plastic flow. Plastic plants often use recycled scrap, which often reflects a tendency to increase viscosity.
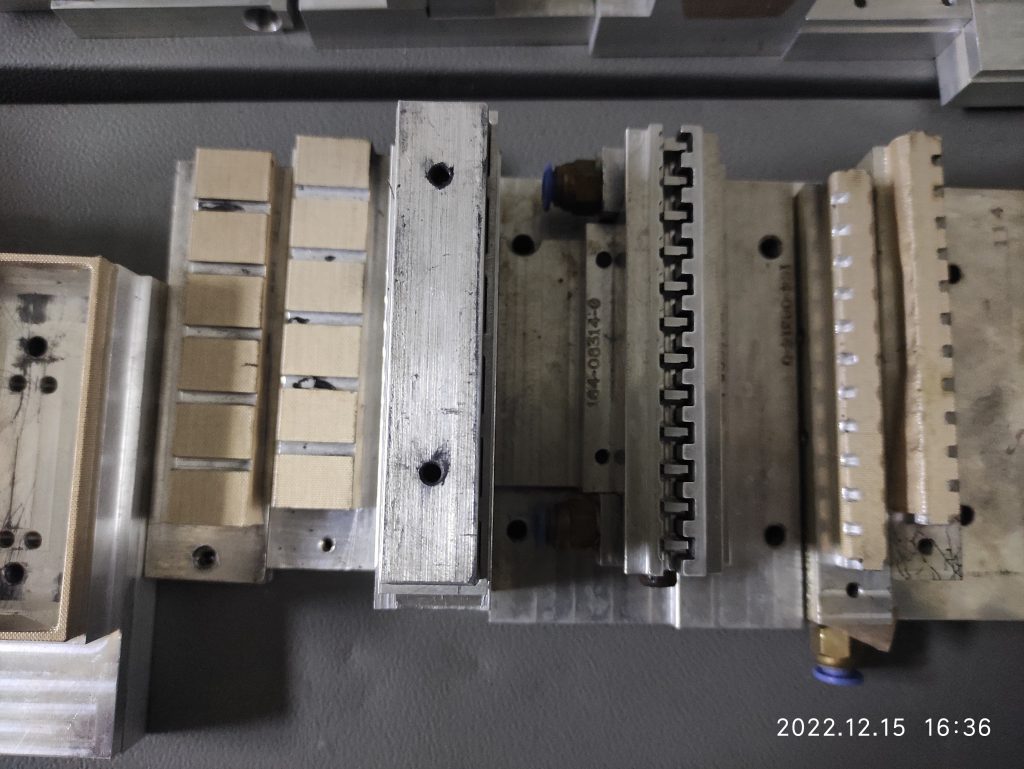