立即联系您的 NewwaySMTC 代表! DuncanLi@newwaysmart.com
载带模具的生产和生产误差的原因
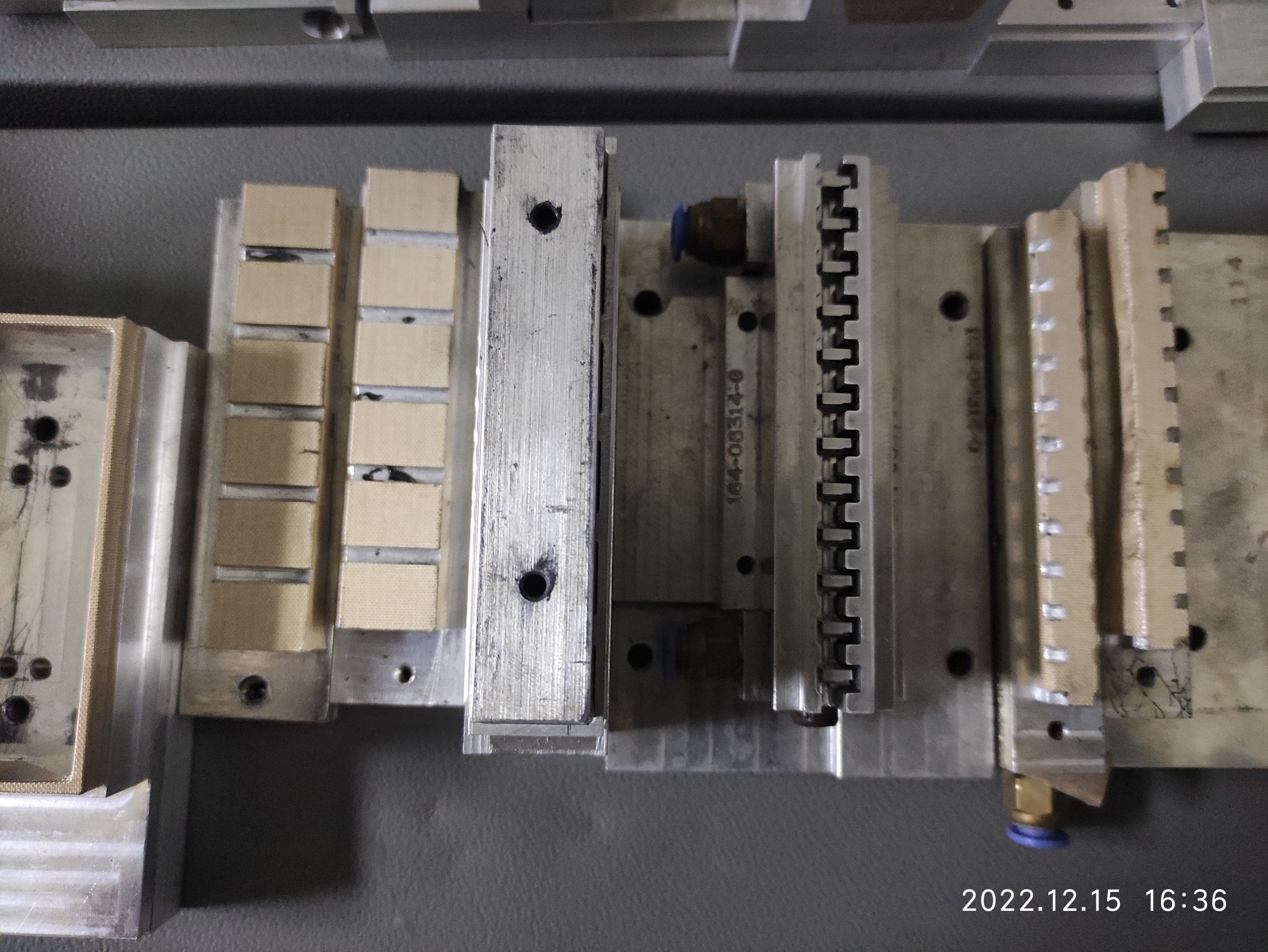
载带模具 可根据载带设计冲孔模具结构,满足市场客户的不同要求,开发出小间隙载带专用全型腔定位冲孔模具,定位准确,操作简单,无需调整任何参数,型腔 P2 值准确到位,解决了众多载带生产厂家的烦恼。
冲压模具寿命长,更换不同规格的底板即可满足一模多用,既高效又省钱。带模具有一模多腔的特点,一次压缩成型可产生约 20 个模腔。
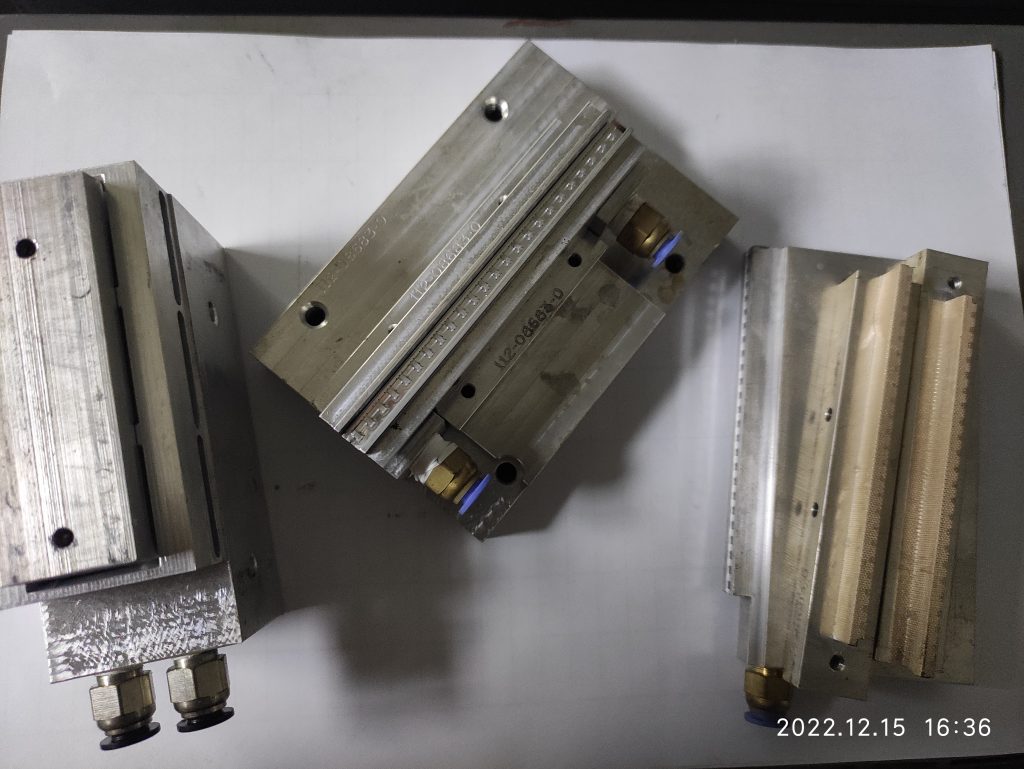
渐进式带模生产工艺 霉菌 技术
SMD 载带 这种试模机械压力机的发展趋势是采用多连杆拉伸压力机,它配有数控液压拉伸垫,具有参数设置和状态记忆功能,在机身制造方面发展很快。
采用渐进式冲压加工转子和定子板材 霉菌或组合拳 霉菌自动冲孔机上的冲压机或其在插入操作中的应用是众所周知的冲压技术。
近年来,级进组合冲压模具开始越来越广泛地应用于车身制造中,在车身制造中,级进模具用于将卷材直接加工成成型件和拉伸件。加工的零件也越来越大,无需使用多工位压力机和成套模具来进行必要的一系列后续工序,如板材剪切、涂油和板坯运输。承载板带模具在美国汽车工业中已得到普遍应用,与多工位压力机上使用的阶梯模具相比,具有生产率高、模具成本低、板材剪切不重要、节省 30% 等优点,但渐进式组合模具技术的应用受拉伸深度、导向和输送板带边缘材料表面硬化的限制,主要用于拉伸深度较浅的简单零件,因此不能完全取代多工位压力机,大部分零件最好在多工位压力机上加工。
板带模具在生产中的重要性
载带模具设计是工业生产的基本生产工艺装备,模具工业是机械工业和高新技术产业的重要组成部分。
载带模具制造过程中的故障
载带模具浇注系统有缺陷。流道太小、太细或太长,增加了流体阻力。可填充空腔
但不能填充其他型腔时,应增大流道直径,以减小熔体流向流道未端时的压降,应增大离主流道较远的型腔浇口,使注入压力和流速达到每个型腔自身相同。
载带模具设计不合理。模具过于复杂,转折点多,进料口选择不当,流道过窄,浇口数量不足或形式不合适。
载带模具制作过程中有哪些错误?
1.进料调整不当、缺料或多料、计量不准确或计量控制系统操作不正常、注塑机或模具或操作条件导致注塑周期不正常、注塑前背压过小或料筒内粒度检查过小。
这可能会导致材料匮乏。
2.注塑压力低、注塑时间短、色谱柱过冷或螺杆过早退出、低工作温度下熔融塑料粘度高、流动性差,应高压高速注塑。
3.注塑速度 huff,注塑速度对于一些形状复杂、厚度变化大、工艺流程长的产品,以及增韧 ABS 等粘度较高的塑料意义重大,当产品不能用高压填充时,应考虑高速注塑。
注射,以克服不尽人意的问题。
4.物料温度过低,料筒前端温度低,讲入型腔的熔体粘度因模具冷却作用而过早上升到难以流动的程度,阻碍远端填充:料筒后端温度低,粘度高,难以流动,遮光
结果,看似压力表上显示的压力足够,但实际上熔体进入型腔的压力和速度都很低,喷嘴温度也很低,这可能是因为固料时喷嘴与冷模的接触时间过长,执行分散。
或因喷嘴加热圈加热不充分或 c 不良导致料温低会堵塞冷模讲料通道:如果模具冷料不好,请使用自锁式喷嘴,并使用后送料程序,在喷嘴能保持必要条件的情况下,只需打开
开机时喷嘴温度太低。有时可以让现场火焰喷枪进行外部加热,以加速喷嘴加热。
5.原料、塑料流动性差。塑料厂经常使用回收的废料,这往往反映出粘度增加的趋势。
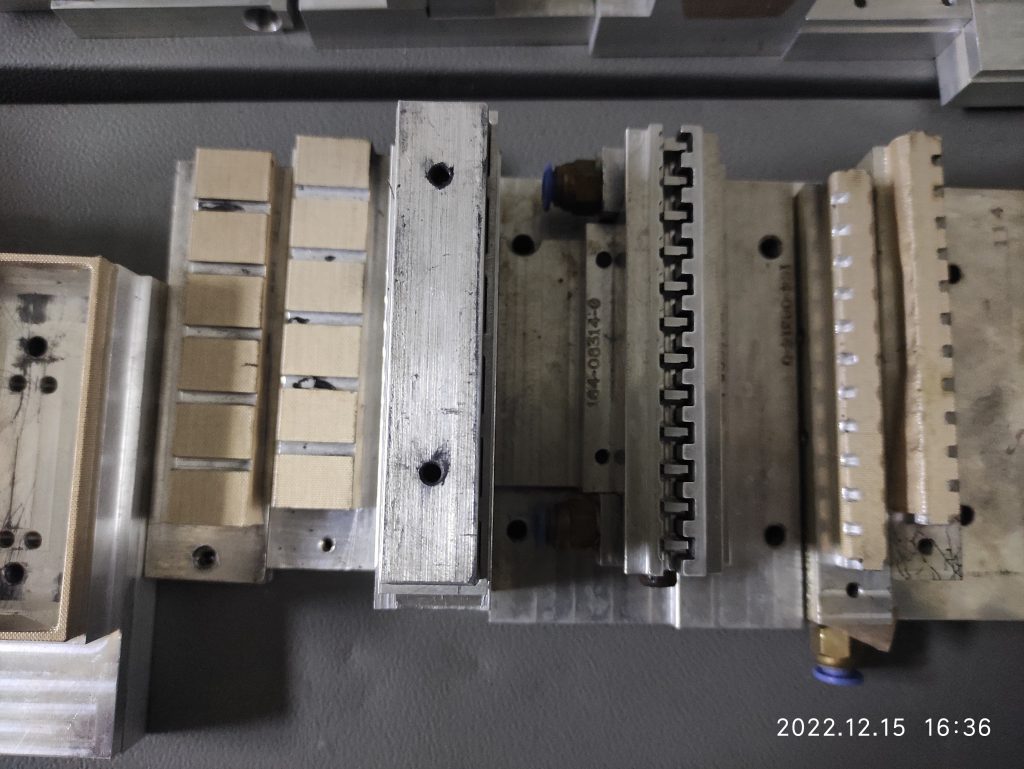